以下文章來源于國家智能制造專家委員會 ,作者中國汽車工程學會
爲進一步助力汽車智能制造發展,中國汽車工程學會數字化與智能制造工作委員會聯合汽車行業國家智能制造示範工廠,總結行業共性需求、技術路線和發展成效,提煉形成汽車行業智能制造典型場景指南,本期典型場景爲數字化工藝設計與仿真。
- 文章信息 -
本文內容來源:中國汽車工程學會。由「國家智能制造專家委員會」原創首發, 數字化企業經授權發布。
01
場景概述
01 / 業務背景
工藝設計是指按照汽車整車産品和零部件産品的設計圖紙、電子樣機以及設計文件要求,設計工藝方案,通過合適的方法、裝備、工具生産出合格産品,如整車生産的沖焊塗總四大工藝等。工藝設計與仿真過程包含工藝分析策劃、工藝方案制定、制造可行性分析、工裝開發/工具選型、工藝驗證與調試、設備選型安裝調試等業務內容。
02 / 痛點需求
隨著汽車産業市場變化和産品更新叠代速度的不斷加快,汽車的生産制造變得愈加複雜,傳統工藝設計和仿真的業務流程和管理模式難以滿足其高質量發展需要,主要表現爲以下兩方面:
(1)傳統的工藝設計模式依賴于人工經驗,難以對複雜工藝流程和多環節交互進行統籌;
(2)工藝仿真環節需要進行大量的試錯實驗,耗費較多時間與資源。
因此,亟需通過數字化的方法和技術賦能傳統的業務流程,支撐數字化工藝設計與仿真場景轉型升級。
03 / 建設內容
汽車數字化工藝設計與仿真場景依托“數字化工藝設計與仿真平台”,通過數據實時共享、數字化生産線和工藝資源庫等數字化工具,對汽車制造過程進行模擬分析、評估優化,設計最佳制造方案,以降低開發成本,減少資源浪費,增強創新能力,加速産品叠代。
04 / 實施步驟
整車企業建設應用數字化工藝設計與仿真場景的周期約18個月,具體實施步驟如下:
(1)前期准備階段:明確實施數字化工藝設計與仿真的實施範圍和目標,制定質量和風險管理策略,制定數字化工藝設計與仿真項目實施計劃;
(2)藍圖規劃階段:設計業務藍圖、制定數字化工藝設計與仿真各模塊詳細方案及實施步驟;
(3)系統實現階段:根據項目範圍建立數字化工藝設計與仿真模型,搭建數字化工藝設計與仿真系統,如圖1所示。
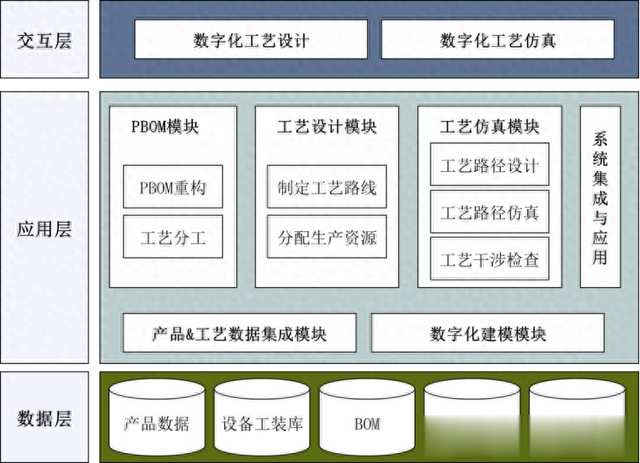
圖1 數字化工藝設計與仿真系統層次架構
05 / 實施基礎
(1)企業/工廠數字化水平和軟件基礎
1)CAD/CAE、CATIA、SolidWorks、NX等産品設計類軟件,用于産品三維設計和建模;
2)CAPP、CAPM、PS等工藝/産線規劃類軟件,用于進行工藝設計、工廠布局和生産線設計三維建模和仿真;
3)MES系統、SCADA系統等生産監控類軟件,用于實時監測和控制生産過程,收集數據並進行分析;
4)PLM、PDM、ERP、CRM等企業管理類軟件,用于管理和跟蹤企業生産過程,協調設計、工藝、采購和生産等環節。
(2)數據基礎
1)産品設計圖紙、電子樣機、技術要求等設計數據;
2)工藝路線、工藝方案、生産線數模、工藝裝備數模、工裝/工具數模等工藝數據;
3)生産線運行過程的實時數據、工藝控制記錄、産品質量監控等過程數據。
(3)硬件基礎
汽車數字化工藝設計與仿真場景的實施不僅需要工作站、高性能計算機、服務器、存儲系統、通信和網絡設備等基礎設施,還需要數據采集感知設備、三維掃描儀和傳感器、虛擬現實和增強現實設備等用于提供直觀的、沉浸式的産品裝配仿真、工藝指導和培訓。
02
典型建設路徑一
長安汽車實踐案例
重慶長安汽車股份有限公司是中國汽車品牌的典型代表之一,長安汽車旗下有長安、深藍、阿維塔、凱程等自主品牌以及長安福特、長安馬自達、江鈴汽車等合資品牌。在當前新一輪科技革命和産業變革中,長安汽車提出並構建了“天上一朵雲,空中一張網,中間一平台,地上全場景”的創新模式。
01 / 場景建設總體框架
長安汽車數字化工藝設計與仿真場景總體框架圍繞業務框架和系統框架兩個部分展開。
(1)業務框架
如圖2所示,業務框架將生産線建設和産品研發兩條路線中的業務內容同步開展。生産線建設階段包含策劃、生産線方案設計、招標定點、概念設計、詳細方案設計、制造安調和應用投産等過程。産品開發階段包括産品數據分析、工藝規劃、分析驗證、詳細方案設計、制造安調、應用投産等。
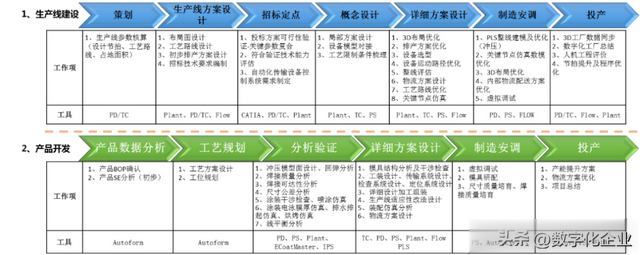
圖2 生産線建設和産品研發同步
(2)系統架構
基于制造數據管理平台中統一的工藝數據,打造智能制造數字化工藝設計管理系統,在線開展同步工程、標准工藝設計,全配置BOM與資源庫、標准工藝關聯,動態生成工藝規程、作業指導書等工藝文件,並實現設計變更和版本管理,如圖3所示。
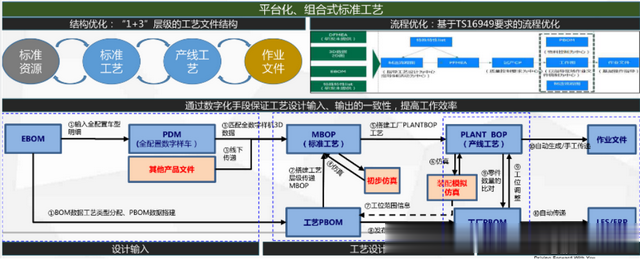
圖3 系統架構
02 / 軟硬件解決方案
長安汽車基于Teamcenter智能制造數字化工藝設計管理系統,集成Tecnomatix仿真軟件,包括PD、PS、Plant、Flow工具模塊,實現産品沖壓、焊接、塗裝、總裝等數字化工藝設計與仿真。如圖4所示。
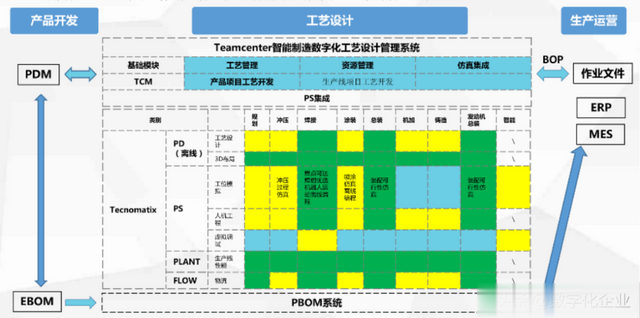
圖4 軟件/平台架構
(1)工藝管理:實現工藝工作流程及工藝文檔實時在線管理,並集成常用辦公軟件,提升工作效率;
(2)資源管理:集成BOM、PDM平台,建立符合工藝的3D數據結構樹,建立統一的數據管理平台,實現基于産品數據、制造數據、工藝標准的工藝設計過程;
(3)仿真集成:集成數字化工藝仿真軟件,實現沖壓線PLS、焊接、塗裝機器人、總裝及發動機裝配、物流等仿真在線分析,動態生成分析報告並與工藝交付關聯,規範分析過程;
數字化工藝設計與仿真場景主要依賴于軟件/系統的設計與開發,場景實施過程中涉及的硬件主要包括工作站和高性能計算機、服務器和存儲系統、通信和網絡設備、數據采集感知設備、圖形加速卡、三維掃描儀和傳感器等。
03 / 業務流程
數字化工藝設計與仿真場景落地實施後,工藝設計與仿真的業務流程如下:
(1)數據收集與准備:從CAD系統、PLM系統、工藝規範等文件中收集數字化工藝設計與仿真所需産品設計數據、工藝參數、設備規格、材料性質等數據;
(2)模型創建與裝配:基于收集到的數據,使用數字化工藝設計與仿真軟件創建産品、設備、工作站等相關模型;
(3)工藝規劃與路徑優化:在創建模型後,進行最佳制造過程、工藝流程和産品組裝順序等工藝規劃與路徑優化;
(4)資源分配與調度:在工藝規劃的基礎上,分配和調度設備、人員和時間等相關資源;
(5)虛擬仿真與驗證:在完成工藝規劃和資源分配後,進行虛擬仿真與驗證。通過在數字化環境中模擬産品制造過程,並根據定義的工藝流程和路徑來驗證其可行性;
(6)性能評估與優化:在進行虛擬仿真和驗證後,對制造過程的制造效率、工時、資源利用、質量指標等進行評估和優化。
04 / 實施成效
實施數字化工藝設計與仿真,同步工程周期縮短30%,工藝規劃效率提升20%。具體表現爲:
(1)通過在虛擬環境中進行設計和仿真,快速評估工藝方案、優化産品設計,有效減少傳統試驗和樣車試制的成本和時間,加速産品研發;
(2)通過優化工藝參數、裝配順序和流程,提高産品質量和一致性,減少産品缺陷,提高産品質量和可靠性;
(3)通過數字化仿真,有助于重塑工藝流程,實現最佳裝配順序,提高生産效率,減少浪費和瓶頸,優化資源利用。
03
典型建設路徑二
東風日産實踐案例
東風日産乘用車公司是東風汽車集團有限公司旗下重要的乘用車事業板塊,是涵蓋企劃、研發、采購、制造、銷售、服務業務的全價值鏈汽車企業,旗下運營日産、啓辰、英菲尼迪三個品牌。
01 / 場景建設總體框架
東風日産的數字化工藝設計與仿真場景實施,從商品企劃開始,伴隨産品開發同期推進。場景建設總體框架包括業務框架與系統框架兩個方面,以業務框架搭載系統框架、系統框架貫穿業務框架的方式建設實施。
(1)業務框架
梳理業務內容,搭建業務框架,如圖5所示。
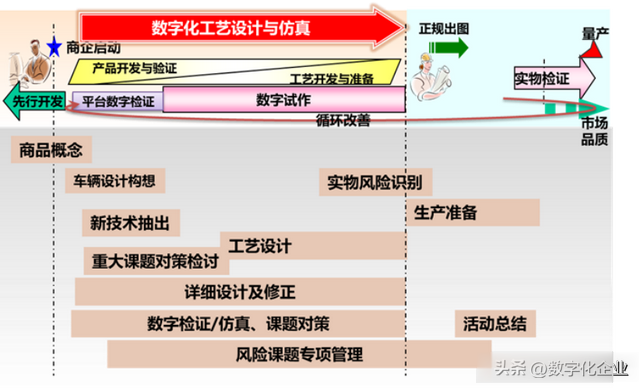
圖5 數字化工藝設計與仿真業務框架梳理
1)將各工程在數字化工藝設計與仿真不同階段的業務內容進行全面梳理,明確線上、線下工作內容;
2)厘清各業務的輸入輸出、輸入來源與輸出對接、業務內運作流程、各工程業務(類似業務),形成流程圖,明確輸入輸出的承接部門;
3)完成輸入輸出以及內部運作的標准化(字段名稱、表格、格式等);
4)按統一數據格式完成相關資源(産線、設備、治工具、模夾檢具、物流包裝、人模特等)的線下數據化。
(2)系統框架
常見的系統框架建設實施有多種方式可選。第一種:各工程根據各自業務特點開發、購買範圍內的系統、軟件等,各業務系統之間進行平台或系統對接。第二種:首先進行平台選擇以及業務規劃,在此平台上進行統一系統開發及各工程軟件工具接入。東風日産采用上述兩種方案結合、以第二種方案爲主的方式構建系統框架,如圖6所示。
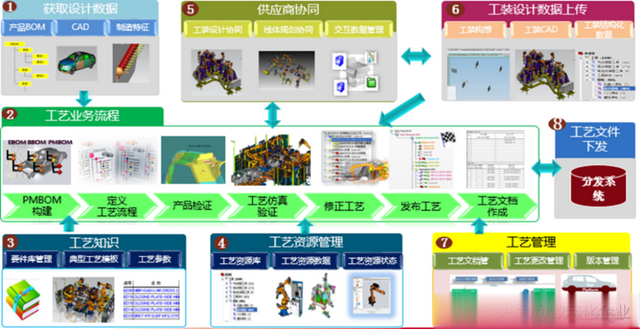
圖6 系統框架
(3)業務-系統結合實施
1)建立産品數據獲取模塊:與設計開發數據系統對接,取得産品設計數據模型;
2)建立工廠資源模塊,根據業務框架的前期梳理搭建工廠資源樹,包括産線、設備、工治具、模夾檢具、物流包裝、物流路線等;
3)建立工序模塊:根據每個車型的制造工序,建立工序模塊,按工序加載以上産品樹及資源樹;
4)工藝文件輸出模塊:通過上下遊系統集成以及工藝文件與工序模塊結合,方便産品數據核對和工藝編制,同時設計變更可及時確認並觸發工藝文件變更。
02 / 軟硬件解決方案
軟件方面:考慮各數字信息的傳輸便利性、信息的唯一性以及維護效率等,平台架構建設將研發設計-制造工藝-工廠制造等功能部門的系統平台進行統一。軟件的選用可以根據各功能部門的需求,統籌使用行業內推薦軟件,在選用的同時必須考慮與平台集成,便于産品數據的及時調用及結果的存儲/引用,如圖7所示。
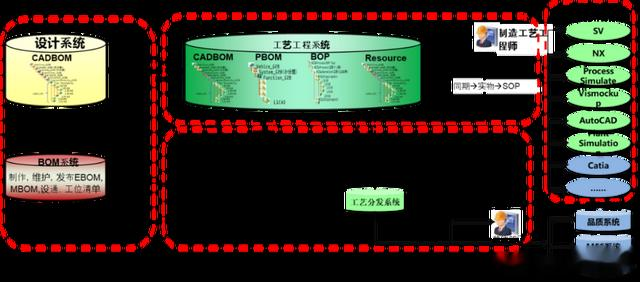
圖7 系統平台架構
硬件方面:汽車行業實施數字化工藝設計與仿真場景應用到工作站和高性能計算機、三維掃描儀和傳感器、虛擬現實和增強現實設備、服務器和存儲系統、穩定的局域網(LAN)或廣域網(WAN)通信和網絡設備等。
03 / 業務流程
從概念設計開始,車型數據、EBOM等從研發系統集成發出,進入工藝工程系統。在工藝工程系統中,車型數據結合工廠資源、工藝標准、工位信息等形成工程工藝樹。各工藝工程根據工藝樹對産品的制造過程進行確認及工藝設計,對不符合項進行整改。最終面向工廠輸出各工藝文件(含工藝參數)以指導産品生産及品質管控。
04 / 實施成效
實施數字化工藝設計與仿真,可以促進新車型准備過程各項指標的提升,主要包括:
(1)品質方面:通過制造過程中的各個驗證環節與産品設計環節同時完成産品制造工藝的設計及虛擬驗證,解決了95%因産品設計與制造工藝沖突而造成的問題,提高制造工藝實施可行性,確保産品量産品質。
(2)成本方面:通過數字化工藝設計與仿真,將産品數據結合制造工藝及産線數據進行仿真,模擬在車型全生命周期範圍內的成本分析及對比,提前確定成本最優方案,使整體車型成本最優。
(3)時間方面:通過品質及成本的提前完成,縮短産品研發周期約20%左右,支撐産品盡早投放市場。(◼️ 本文完)